This article is created by The Better India and sponsored by WingifyEarth
Autokast Ltd, a government of Kerala undertaking, is using its waste foundry sand to make eco-friendly and low-cost silica bricks. The unit is built with a capacity to produce 4,000 bricks per day.
Someone once said that “One man’s trash is another’s treasure,” and setting yet another example of how, is the Kerala government undertaking Autokast Ltd, a ferrous foundry manufacturing unit.
As per a 2021 report by The Hindu, the company generates 700 tonnes of foundry waste sand every month. They have innovated a technique that will help convert sand into bricks that can be used by the construction sector. This was developed by the CSIR-National Institute for Interdisciplinary Science and Technology (NIIST) at Pappanamcode in Thiruvananthapuram, Kerala.
“A team from CSIR-NIIST, the technology partner of the project, is expected to visit Autokast Ltd this week. They will make 3,000 bricks in our presence as part of transferring the technology. We will pay a fee for using their technology,” said V K Praviraj in a 2022 report to The Hindu.
The manufacturing unit is built with a capacity to produce 4,000 bricks per day. While initially, the production will be around 1,500 bricks per day, the unit will reach its full capacity over a period of time, the report says.
“The bricks made from silica sand are eco-friendly and we expect the product will be well received by the market,” said an official of Autokast Ltd.
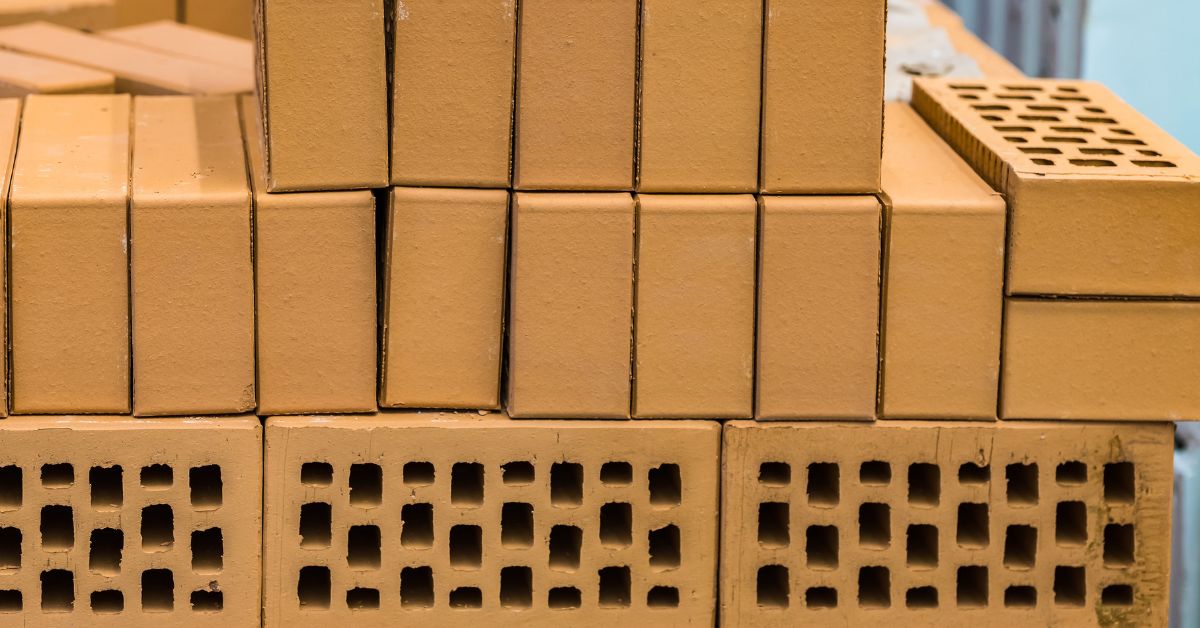
The manufacturing unit is built with a capacity to produce 4,000 bricks per day. (Representational image: Shutterstock)
Why Silica bricks?
A common issue that growing economies like India deal with is the rising population and subsequent damage to the environment to meet the demands of said population.
A research paper by Mckinsey & Company titled Environmental and Energy Sustainability: An approach for India predicts “the building construction sector in India would grow at a rate of 6.6% per year till the period 2030 since 80% of India is yet to be built”.
The constant growth in the construction industry is bound to increase demand for construction materials, especially bricks. To meet this demand, the foundry industries indulge in mass production leading to mass waste generation.
“The disposal of waste sand in the environment, typically in landfills, causes direct contamination of soil due to metals. It may also contaminate the groundwater resources and surrounding superficial environment,” the paper states.
The Mckinsey & Company report also suggests that the penetration of toxic materials in the soil and especially groundwater can lead to water-borne diseases.
“Studies show that WFS (waste foundry sand) can be used in the manufacturing of clay bricks. Recycling of foundry sand residuals as aggregates in the manufacture of red clay bricks and tiles was studied. Clay bricks were prepared with 10%, 20%, 30%, 40%, and 50% of WFS. It was reported that the best results were obtained in samples with 30% and 40% WFS,” the report observes.
As per Autokast Ltd, as well as research around the subject, Silica bricks are more eco-friendly and save tonnes of WFS from being dumped in landfills.
A Science Direct research paper suggests that the process of making bricks involves combining clay-sand mixtures, forming bricks, and drying and firing the bricks. They are most commonly used as refractories as the bricks are “low cost, have high creep resistance and cause low pollution”.
On a path of setting an example for other manufacturing units to save the environment one silica brick at a time, the project was undertaken as part of the ‘Waste to Wealth’ research programme of the Council of Scientific and Industrial Research (CSIR).
The Hindu report states, “The cement bonding and compression moulding technique can produce high-strength bricks that meet the IS 1077 standards, and they can be produced in aesthetically appealing colours to suit interior designing requirements, according to NIIST scientists.”
Leave A Comment
Your email address will not be published. Required fields are marked.